PP管材擠出成型時易出現哪些問題
PP管材擠出成型過程中的常見問題及解決方案
在塑料加工行業中,PP管材因其******的耐腐蝕性、耐磨性、耐高溫性和******的電***緣性能而被廣泛應用。然而,在PP管材的擠出成型過程中,可能會出現一些問題,影響產品的質量和生產效率。本文將詳細介紹這些可能出現的問題及其解決方案。
1. 管材表面粗糙:這可能是由于模具內部有雜質,或者模具溫度過高導致的。解決方法是定期清理模具,確保模具內部清潔;同時,適當降低模具溫度,避免因溫度過高導致管材表面粗糙。
2. 管材彎曲:這可能是由于冷卻不均勻或者牽引速度過快導致的。解決方法是調整冷卻系統,確保冷卻均勻;同時,適當降低牽引速度,避免因速度過快導致管材彎曲。
3. 管材壁厚不均:這可能是由于模具設計不合理或者擠出機螺桿磨損導致的。解決方法是***化模具設計,確保模具能夠保證管材壁厚的均勻;同時,定期檢查和更換擠出機螺桿,避免因螺桿磨損導致管材壁厚不均。
4. 管材內外壁粘連:這可能是由于冷卻時間不足或者冷卻水溫度過高導致的。解決方法是延長冷卻時間,確保管材內外壁充分冷卻;同時,適當降低冷卻水溫度,避免因溫度過高導致管材內外壁粘連。
5. 管材斷裂:這可能是由于原料水分過高或者擠出機壓力過***導致的。解決方法是控制原料的水分,確保原料水分在合理的范圍內;同時,適當降低擠出機的壓力,避免因壓力過***導致管材斷裂。
6. 管材顏色不均:這可能是由于原料混合不均或者擠出機溫度不穩定導致的。解決方法是***化原料的混合過程,確保原料混合均勻;同時,調整擠出機的溫度控制系統,確保擠出機的溫度穩定。
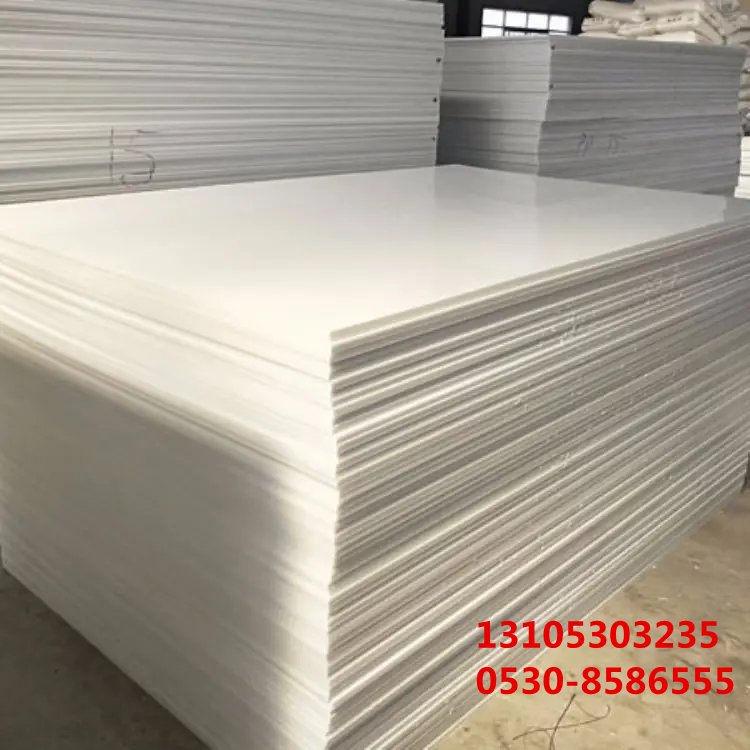
總的來說,PP管材擠出成型過程中的問題主要涉及到模具、冷卻系統、牽引系統、擠出機等多個方面。解決這些問題需要從多個角度進行,包括***化模具設計、調整冷卻系統、***化牽引系統、定期檢查和更換擠出機等。只有這樣,才能確保PP管材的質量和生產效率,滿足客戶的需求。