探究PP管材注塑過程中引起分解的原因
探究PP管材注塑過程中引起分解的原因
在塑料制品的生產(chǎn)中,聚丙烯(PP)管材因其***異的性能和成本效益而廣泛應(yīng)用于各個***域。注塑成型作為一種高效的塑料加工方法,其生產(chǎn)過程的穩(wěn)定性對產(chǎn)品質(zhì)量至關(guān)重要。然而,在PP管材的注塑過程中,材料分解現(xiàn)象時有發(fā)生,這不僅影響產(chǎn)品的外觀和性能,還可能導(dǎo)致生產(chǎn)成本的增加。本文將詳細(xì)探討PP管材注塑中引起分解的原因,并提出相應(yīng)的解決策略。
一、熱分解
PP材料在高溫下容易發(fā)生熱分解,尤其是在注塑機(jī)的料筒中長時間受熱。當(dāng)溫度超過PP的熔點(diǎn)時,分子鏈開始斷裂,導(dǎo)致材料的降解。為了避免熱分解,需要嚴(yán)格控制注塑溫度,并確保材料在料筒中的停留時間盡可能短。
二、剪切應(yīng)力
在注塑過程中,PP熔體通過噴嘴和模具的流動會產(chǎn)生剪切應(yīng)力。過高的剪切應(yīng)力會破壞PP的分子結(jié)構(gòu),引起材料的降解。因此,合理設(shè)計(jì)流道系統(tǒng),減少流動阻力,以及選擇合適的注塑參數(shù),是防止剪切引起分解的關(guān)鍵。
三、氧化降解
PP材料在加工過程中暴露在空氣中,容易與氧氣發(fā)生反應(yīng),導(dǎo)致氧化降解。這種降解通常伴隨著材料的變色和力學(xué)性能的下降。為了減少氧化的影響,可以在注塑過程中使用抗氧化劑,同時確保注塑環(huán)境的密封性,減少空氣接觸。
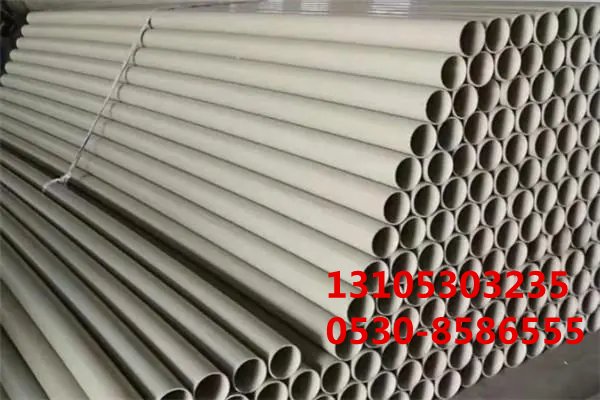
四、水分引起的降解
PP材料吸濕性較低,但在潮濕環(huán)境中仍可能吸收少量水分。在注塑過程中,這些水分可能會在高溫下轉(zhuǎn)化為蒸汽,導(dǎo)致內(nèi)部氣泡的形成,影響產(chǎn)品的質(zhì)量。因此,在加工前對PP材料進(jìn)行適當(dāng)?shù)母稍锾幚硎欠浅V匾摹?/div>
五、雜質(zhì)和添加劑的影響
PP管材在生產(chǎn)中可能會添加各種助劑,如穩(wěn)定劑、增塑劑等。如果這些添加劑的質(zhì)量不佳或添加比例不當(dāng),可能會導(dǎo)致材料的不穩(wěn)定性,從而引起分解。此外,原材料中的雜質(zhì)也可能成為分解的潛在因素。因此,選擇高質(zhì)量的原材料和添加劑,以及***控制添加比例,對于保證注塑過程的穩(wěn)定性至關(guān)重要。
結(jié)論:
PP管材在注塑過程中的分解是一個復(fù)雜的問題,涉及到多種因素。通過對上述原因的分析,我們可以得出一些預(yù)防措施:嚴(yán)格控制注塑溫度,***化流道設(shè)計(jì),使用抗氧化劑,確保材料的干燥處理,以及選擇高質(zhì)量的原材料和添加劑。通過這些措施,可以有效避免PP管材在注塑過程中的分解,提高產(chǎn)品質(zhì)量,降低生產(chǎn)成本。